Ford news
Ford Struandale Engine Plant: Using the World’s Best Practices to Optimise Export-driven Manufacturing
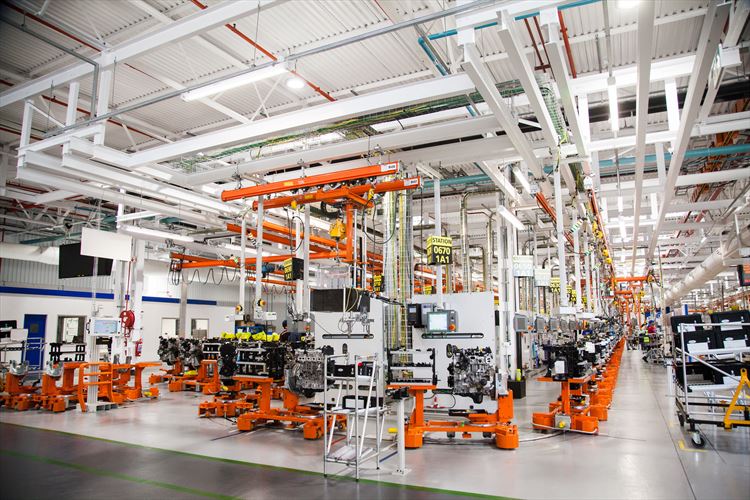
Ford Struandale Engine Plant: Using the World’s Best Practices to Optimise Export-driven Manufacturing
- The Ford Struandale Engine Plant in Port Elizabeth is one of the Eastern Cape’s top exporters, having won its fourth annual Exporter of the Year award from Exporters Eastern Cape this year
- As part of Ford’s global supply chain, the Struandale Engine Plant produces machined components and fully assembly engines for the domestic market, as well as direct and indirect exports
- Using the principles of Six Sigma and Lean Manufacturing helps the plant find the perfect balance of delivering world-class products on time, at the right quality and at the lowest cost
PORT ELIZABETH, South Africa, 18 September 2020 – Ford Motor Company of Southern Africa’s Struandale Engine Plant, based in Port Elizabeth, is renowned as one of the Eastern Cape’s leading exporters, having recently won its fourth Best Exporter OEM award from Exporters Eastern Cape.
It is also an integral part of Ford’s global supply chain with machined components and fully assembled engines produced for the domestic market, direct exports of engines and components to Ford plants around the world, and indirect exports as the sole provider of engines fitted to the Ranger pickup produced at the Silverton Assembly Plant and shipped to over 100 global markets.
In a highly complex global automotive industry, achieving this status is no small feat, requiring an unwavering focus on production efficiency and quality, with the ultimate aim of delivering exceptional customer satisfaction.
“There are two primary objectives in manufacturing, and these are to be the lowest-cost producer at the highest quality,” explains Shawn Govender, Plant manager of the Struandale Engine Plant. “Successful manufacturing operations can only achieve this by being the best at what they do, and it’s a goal that we strive towards daily in order to remain relevant and competitive on a global scale.
“We rely on two distinct but complementary processes that are synonymous with Ford’s manufacturing operations internationally, which are Six Sigma and Lean Manufacturing,” Govender says. “Six Sigma is a business process that enables companies to increase profits by streamlining operations, improving quality and eliminating defects or mistakes in everything they do.”
The Six Sigma certification incorporates several skill levels, with employees starting off with Yellow Belt status and a basic understanding of the Six Sigma principles. Those who have attained Green Belt status assist with data collection, analysis and supporting the projects. Black Belt-certified staff are trained in the Six Sigma strategy and tools, and deploy projects by leading teams of employees through a defined process to eliminate product and process variation – which, in turn, helps spread the knowledge to other members of the organisation. A Master Black Belt trains and coaches the other tiers, and functions at the Six Sigma program level.
It’s a topic that Govender knows well, as he became the first representative from Ford Motor Company of Southern Africa (FMCSA) to achieve Six Sigma Black Belt certification more than two decades ago following extensive training at Ford in the US, Germany and Thailand. He subsequently attained his Master Black Belt status, and is busy with his Doctorate at Nelson Mandela University, focusing on the development of a quality and efficiency improvement model for complex manufacturing industries.
“Traditional quality programmes focus on detecting and correcting defects, whereas Six Sigma encompasses a broader approach that provides specific methods to recreate the process itself so that defects are eliminated,” Govender elaborates.
“Six Sigma helps establish a course and gauges the pace in the race for total customer satisfaction. It is a crucial tool that assists the company in gaining the competitive edge by improving quality and delivering greater customer satisfaction, which consequently translates into business growth and higher employment levels.”
The Science of Lean Manufacturing
“Lean manufacturing is a science, with a clear best-practice method that must be deployed to deliver the optimal results,” Govender states. “We use the Ford Production System (FPS), which is the company’s gold standard for all its manufacturing operations around the world and, along with Six Sigma, is also used at our Silverton Assembly Plant in Pretoria. The objective of FPS is to achieve a lean, flexible and disciplined production system that is common to all Ford plants, regardless of their location or the products manufactured.”
FPS has specific focus areas and metrics relating to safety, quality, delivery, cost, people, maintenance and the environment (abbreviated as SQDCPME), which are used to continuously guide, measure and improve each aspect of the business. Integrated into these principles are specifically developed and integrated operating systems linked to the global Ford IT network, which gives every team member access to detailed scorecards that identify any issues impacting the plant’s performance.
“Essentially, the Ford Production System focuses on the ‘flow’ of the plant, deploying a structured approach to manufacturing that clearly maps out what we should be doing, how we should do it, and validating if what we are doing is correct and in line with FPS requirements,” he adds. “This is crucial in avoiding stopping the production line for defects, reworks or maintenance issues, and reduces the level of scrap,” he says.
Key metrics within FPS are first time through (FTT), which measures how many goods are produced correctly without any defects or rework as a percentage of the total units manufactured, and rolled throughput yield (RTY) that indicates the probability of a single unit passing through a series of processes free of defects. These metrics are fully integrated into Ford’s systems, as they provide important indicators of the compliance and capability of the manufacturing process.
“Within manufacturing, we are constantly working on ways to improve the capabilities of our processes, using the principles of Six Sigma and the Ford Production System to create a leaner, more cost-effective and quality-driven business,” Govender says. “This focus on continuous improvement and lean manufacturing empowers every Ford employee to make a meaningful contribution to the company’s success, and help achieve our objectives of delivering world-class products on time, at the right quality and at the lowest cost.”
# # #
Read the latest news from Ford South Africa by visiting the Newsroom:
https://www.ford.co.za/about-ford/newsroom/
Original article and image as supplied by QuickPic